前言:
大板生产:石材荒料经过锯切成所需厚度的毛板,再经过胶补、抛磨后达到一定饰面效果的过程。
大板分类:大理石和花岗石大板两大类。
大板的生产工艺流程:选料——整形——锯切——胶补——抛光——检验——包装——入库。
大板加工设备:整形机、框架锯、砂锯、胶补线、连续自动磨机。
辅助设备:翻板机、大板车、单梁臂吊车、双(单)梁行车、龙门吊车等。
一、选料:
原则:同一工程用料的大板基本保持颜色、纹向、花纹基本一致的原则
方法:用目测法、水浇法判断荒料等级。
二、整形
3.1大理石锯切荒料的长*宽*高尺寸,不能超过3300*2000mm*2000mm,花岗石荒料最大加工尺寸:3300*3500*2000 mm,超出部分要先进行整形。
3.2荒料长、宽、高方向有不规则或底面、端面不平,则首先修整底面。
3.3为提高荒料利用率及板材利用率或者按加工单要求整形。
3.3.1色斑、色线、阴阳色在荒料中间位置且与大面基本平行,宽度≥200mm时应分段处理。
3.3.2色斑、色线、阴阳色在荒料一端规格在400mm * 400mm * 400mm以上时,应作分切处理。
3.3.3材料有严格方向性时,对色斑、色线、阴阳色应请示相关领导及业务作相应的处理。
4.对材质较松、有暗裂的材料(如深啡网、金蜘蛛、紫罗红、雨林啡、玛雅米黄、玉石等)、根据荒料裂纹情况分切处理。
5、保证整台车荒料配满时需对荒料进行分切后配料,由车间主管及班长根据情况确定分切方案。
6、遵循荒料硬度基本一致、长度尺寸基本一致、高度尺寸基本一致,保证整车荒料最大加工尺寸的原则。
三、锯切
框架锯:用来锯切大理石荒料的设备,主要由主电机、大飞轮、连杆、框架结构、荒料车升降台、传动系统、液压张紧及润滑系统、冷却水系统和面板控制系统组成。
工作原理:通过主电机带动大飞轮的转动,再带动锯框上的锯条做水平往复运动,利用锯条上的金刚石刀头将荒料在冷凝水的冷却情况下切割,切割时荒料随工作台由下向上进给。框架锯可以加工10 -40 mm厚大板。
砂锯:是用来锯切花岗石荒料的设备,主要由主电机、大飞轮、连杆、锯条框架结构、荒料车、液压张紧系统、供砂系统、砂浆喷淋系统和面板控制系统。
工作原理:通过飞轮的转动,带动锯条水平往复运动,利用砂浆里的石灰水和多棱钢砂,对荒料进行切割,切割时锯条随框架由上向下移动。
锯切前荒料的检查、防护:
1、检查荒料,根据纹路走向、缺陷的回避程度、板面大小等因素,确定加工方向,查看是否有加工隐患,避免在锯切时损坏锯条和设备。
2、有裂纹的荒料,应在荒料顶部和两端面、底面用AB加厚网或者粘石板;孔洞多、裂纹多的荒料要灌胶和粘石板或者加厚网处理;
3、裂纹特多的大理石估计无法退锯片的荒料,在上料时底部要加水泥垫石再上锯加工。
4、出材率:
大理石
20mm 42.5m2/m3
25 mm 34.5 m2/m3
30 mm 29 m2/m3
锯缝 4.0 mm--4.5 mm (850左右-----厚度乘以出材率)
花岗石
20 mm 36.5m2/m3
25 mm 30m2/m3
30 mm 25m2/m3
锯缝 7.5 mm (750左右-----厚度乘以出材率)
每立方米出毛板的出材率,计算方法=1000M3/(板厚+锯缝),锯缝的大小由锯片厚度和刀头尺寸决定。
5、加工周期:
大理石每车料加工12-15小时,每车料加工20mm厚毛板约250-300m2,框架锯每月产量约45000m2,加工周期:从荒料到光板约3天时间;
花岗石每车料锯切3-5天,每车料加工20 mm厚毛板约500 m2,8台框架锯每月产量约20000 m 2,加工周期:从荒料到光板约5-7天时间。
6、大理石锯条、间隔片的选择:
大理石框架锯目前使用的锯条锯条规格:4350mm(4200mm)*180mm*厚度,厚度有三种规格:3.5 mm 、2.5 mm、2.0 mm,1.5 mm。深啡网用3.5mm专用刀头、刀体加工,四类较硬材质荒料用2.5刀体加工(伯利黄),其它普通材质的米黄三类荒料选用2.0 mm的刀体加工(莎安娜、罗马米黄),较软一类材质荒料用1.5刀体加工(白砂石、银河白等),新刀头在加工10000至15000平方后,要进行二次调整间隔片的厚度。
具体配置方法见下表:
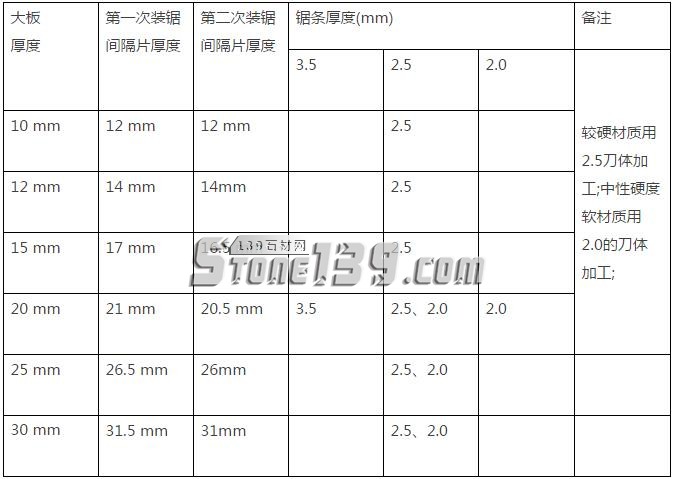
7、框架锯操作注意事项:
7.1把荒料车上升工作台至荒料的最高点与刀齿相距约5 mm,然后开动机器,进行加工,锯切过程中大板厚度的检查和加固。
7.2在荒料的锯切过程中为防止偏刀,进给速度分三个阶段,即起始速度、中间速度和结尾速度,起始速度和结尾速度是中间速度的一半。从起台速度到中产速度过程要分3次完成,切忌一次性加速到中间速度。
大理石锯机锯切加工参数对照表
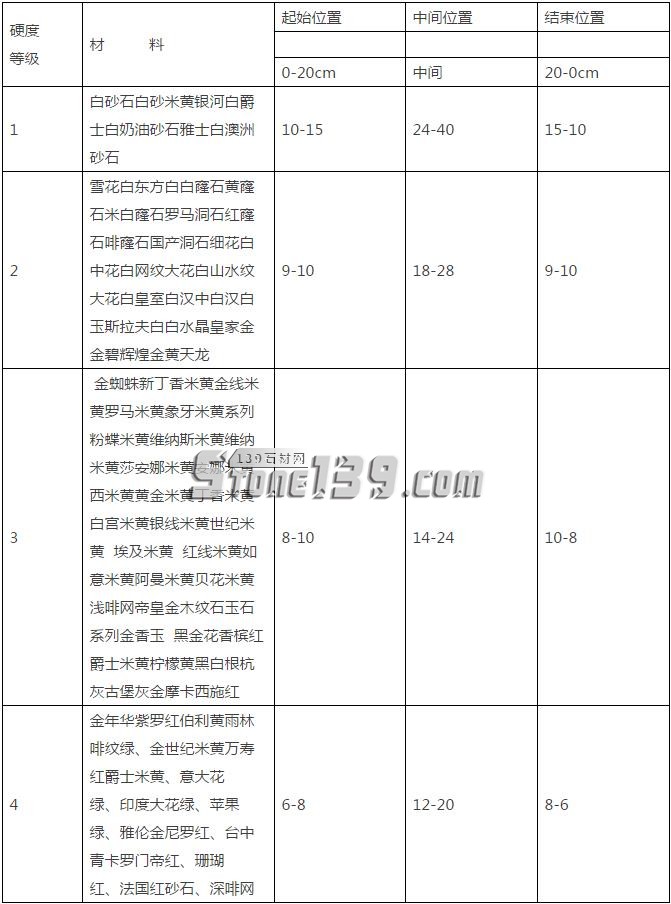
7.3锯条的使用情况分析:通过查阅锯条使用记录分析刀头的锋利度(切割速度)、耐磨度(切割面积),偏刀、锯条断裂、掉刀头等综合判定。
8、砂锯锯条有两种规格:3830*100*4.2 mm和4230*100*4.2 mm
8.1根据加工单要求和使用的钢砂锯条,按下表选用间隔片:
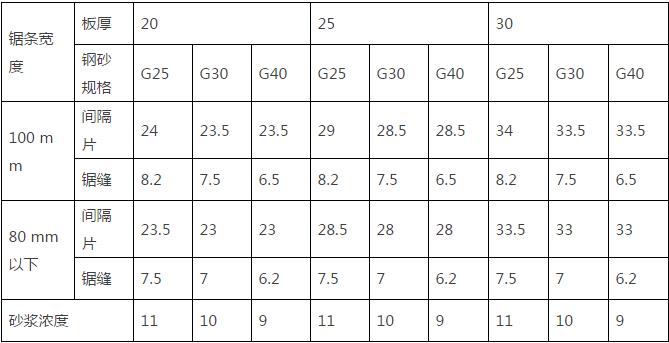
8.2砂锯锯切加工注意事项:
锯机在加工过程中,操作人员要对自己的机台砂浆进行认真的检查、检测。开机0.5小时内必需对机台砂浆检测,以后每2小时测量一次。检测项目:比重、浓度、砂量、检查张力。砂浆浓度为1700-1900克/升,中间锯切速度为20-42mm/h,总砂量在180-300克/升。金年华、紫罗红、雨林啡此几种大理石是用砂锯加工的。
四、胶补
胶补是大板加工中很重要的一个技术环节,胶补质量的好坏直接决定了板面的质量,并对出材率和大板级别有影响。
1、常用胶的品种:
胶补所需的主要胶料有:AB胶、树脂胶3388#、树脂胶191#、雅科美胶、大力士云石胶等。
2、胶补的原则:多补石粉、石粒、少补胶
胶水调色的基本原则:避难就易,如板面没有明显花纹,胶水颜色随板面的颜色,如花纹明显,胶水颜色随花纹的颜色。调胶是胶补工作中的重要环节,直接影响到胶补质量。
3、胶补分加网和刮面两道工序(略)
五、抛光
1、抛光的定义:抛光是通过电机带动磨盘上的磨料高速旋转后连续对毛板进行磨削,从而达到一定的镜面光泽度或其它的板面效果的过程。
2、抛光机结构:有工作台、主轴电机、摆桥、皮带传输系统和面板控制系磨盘和液、气压系统组成。
3、上板:将需要抛光的板材转运到抛光机上板处的A字架上,板材在上板处放置时,要网面向外。板材未加网的,则要选择板面较好的一面作为光面,有明显纹路的要选择左旋方向为光面。
4、上板前要检查板材加网面有无胶粒、胶块及凸出不平的地方
5、根据板材的软硬程度,对各磨头的磨料进行排序设置及压力调整,具体参数为:桥速度26-31m/min,皮带速度60-150mm/min,压力范围在0至6kg之间。
6、工作中,要经常检查磨头运行情况,若发现磨头摆动过大,需停机检查。磨料更换时,要一次性更换整组磨料,以保证整组磨料厚度一致。
7、磨机可以加工的板面效果:光面、哑光面、仿古面。
10、花岗石的磨机使用方法基本同大理石相同。
大板抛光注意事项:
1、对花磨:相邻两件大板按锯机原始编号进行正反面抛光的方法,大板合、分扎时需严格按原始编号顺序,以保证追纹效果。
2、白色类石材抛光后放置时,板与板之间需用0.03mm厚的塑料薄膜隔离,以免污染板面(洞石类除外)。
3、网面撒石粉抛光后的大板需光面对光面放置,以免划伤板面。
六、检验:
七、包装:成品大板用木架包装的过程。
八、入库:由收方员计算、记录,质检员核定大板面积、定级别后输入电脑做账,交仓库管理的过程。
九、板材饰面效果:
1、工程板板面效果分类:镜面板、哑光板、粗面板。
光面、哑光面、仿古面、仿古面釉面、火烧面、火烧仿古面、荔枝面、拉丝面、刀切面、剁斧面、水洗面等、喷沙、酸洗面、酸洗仿古面、菠萝面、开裂面、蘑菇面。
2、天然石材常见的表面加工方法
光面:表面非常的平滑,高度磨光,有镜面效果,有高光泽。花岗岩、大理和大理石通常是抛光处理,大理石光泽度平均在80度,花岗石在90度以上,并且需要不同的维护以保持其光泽。
哑光:表面平滑,但是低度磨光(10-40度左右),产生漫反射,无光泽,不产生镜面效果,无光污染。
仿古:模仿石材使用一定年限后的古旧效果的面加工,一般是用仿古研磨刷或是仿古水来处理,模仿石头自然的磨损效果。表面光泽度约10度左右,一般仿古研磨刷的效果和性价比高些,也更环保。
仿古面釉面:表面光泽度约40度左右的仿古面。
火烧面:表面粗糙。这种表面主要用于室内如地板或作商业大厦的饰面,劳动力成本较高。高温加热之后快速冷却就形成了火烧面,火烧面一般是花岗岩,部分大理石也加工火烧面(如伯利黄)
火烧仿古:先火烧后再做仿古加工。
荔枝:表面粗糙,凹凸不平,是用凿子在表面上密密麻麻的凿出小洞,有一模仿水滴经年累月的滴在石头上的一种效果。
拉丝面:在石材表面上均匀开一定的深度和宽度的沟槽。
刀切面:直接由圆盘锯、砂锯、框架锯或桥切机等设备切割成型,表面较粗糙,带有明显的机切纹路。
剁斧:也叫龙眼面,是用斧剁敲在石材表面上,形成非常密集的条状纹理,有些像龙眼表皮的效果。
水冲面:用高压水直接冲击石材表面,剥离质地较软的成分,形成独特的毛面装饰效果。
喷沙:用普通河沙或是金刚沙来代替高压水来冲刷石材的表面,形成有平整的磨沙效果的装饰面。
酸洗:用强酸腐蚀石材表面,使其有小的腐蚀痕迹,外观比磨光面更为质朴。大部分的大理石都可以酸洗,酸洗也是软化花岗岩光泽的一种方法。
酸洗仿古:先酸洗后再做仿古加工。
菠萝:表面比荔枝加工更加的凹凸不平,就像菠萝的表皮一般。
开裂:俗称自然面,其表面粗糙,不过不像火烧那样粗糙。这种表面处理通常是用手工切割或在矿山錾以露出石头自然的开裂面。
蘑菇面:一般是用人工劈凿,效果和自然劈相似,但是石材的天面却是呈中间突起四周凹陷的高原状的型状。